Girls Who Code
Ring-A-Thing Introduction
The
Ring-A-Thing is a modular ring-building kit that allows you to press-fit a small cube magnet into the base and top parts of your ring, enabling you to switch out designs on your printed ring. Be a new superhero every day, change your ring with your mood or the season, etc.
This project is a derivative of
IWorkInPixel's Ring-a-Thing TBuser's Ring-A-Thing w/ Pin Connectors Cymon's TARDIS Ring-a-Thing
OpenSCAD
OpenSCAD is software for creating solid 3D CAD objects. It is free software and available for Linux/UNIX, MS Windows and Mac OS X.
OpenSCAD is good for creating 3D models of machine parts or any part where you want to specify parameters.
OpenSCAD is not an interactive modeller. Instead it reads in statements that describes the object and then it renders the 3D model from that code. This gives you full control over the modelling process and enables you to easily change any step in the process or make designs that are defined by configurable parameters.
OpenSCAD provides two main modelling techniques:
- Constructive Solid Geometry
- Extrusion of 2D outlines
Numbers in OpenSCAD are in millimeters. So
circle(5); or
circle(r=5); draws a circle with a radius of 5mm.
Here is the code for the base of the ring. Measure the diameter of your finger at the largest part and pass in that value. If you want a delicate ring, the second parameter should be set to true.
$fn=100;
magnet=3.4;
ring_size = 18;
rotate([0,0,90])
ring(ring_size, true);
module ring(size, d=true) {
difference() {
union() {
cylinder(r=size/2+2, h=9, center=false);
translate([0, size/4+2.5, 9/2])
if(d){
cube(size=[size, size/2+4, 9], center=true);
}else{
cube(size=[size+4, size/2+4, 9], center=true);
}
}
translate([0, 0, -1])
cylinder(r=size/2, h=12+2, center=false);
translate([-1.5, size/2+1.5,2.5])
cube(magnet);
}
}
When you have configured your ring press
F5 to compile the image. If everything looks good, press
F6 to compile and render—build the mesh.
After your mesh is created select
Export as STL from the
Design menu.
STL or
STereoLithography files describe the surface geometry of a 3D object and are used to build physical 3D CAD Models.
stl files are created using a mesh made of triangles that represents the physical part of your object. The STL file is a complete listing of the xyz coordinates of the vertices and normals, the vectors perpendicular to a surface that determine the orientation for the triangles, that describe the 3D object.
A good STL file size is between .5MB for a simple file to 10MB for a large complicated one. Generally, if your part is outside of these parameters, you'll need to resize it. A good STL file must also conform to two rules.
-
Adjacent triangles must have two vertices in common
- The orientation of the triangles (what side of the triangle is in and what side is out) as specified by the vertices and normals must agree
Minor gaps and inconsistencies can usually be fixed by specialized STL-handling software. If you have more significant problems, you'll have to go back to your original CAD model.
An STL file can be termed bad because of translation issues. In many CAD systems, the number of triangles that represent the model can be defined by the user. If you are using too many triangles, the stl file size can become unmanageable. If you're using too few triangles to describe your object, your curved areas will not be properly defined and your cylinders might look like hexagons.
Generating GCode
So you have an STL file. Now what?
Once you have a
STL file, the 3D model needs to be sliced into layers in order to be printed. The software that slices a model is called
SkeinForge, and it is incorporated into
ReplicatorG, which translates the 3D information into
GCode, the common name for the widely used
computer numerical control (CNC) programming language). The
GCode tells the
MakerBot how to print the object.
Here are the basic steps involved in printing:
- Start with an STL file
- Open ReplicatorG
- Open the STL file in ReplicatorG
- Generate the GCode file
- Either use an SD card or connect your computer to the MakerBot using a USB cable.
- Print!
Printing your ring
The base of the ring is a simple model and there is little chance that something is wrong with the file. In this case you will open the file up in ReplicatorG.
- Open ReplicatorG
- From the File menu, select Open and navigate to your STL file.
- Click on the Move Button

- Next select Center and Put on Platform
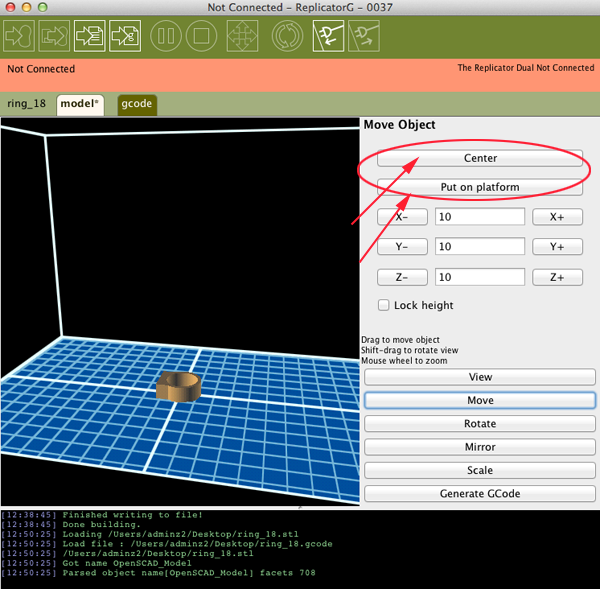
- You could now may other adjustments like rotating, mirroring and scaling, but for the ring, we'll just leave it as is.
- Now click on the Generate GCode button

You will be prompted to confirm that you want to save the changes you made. Click on Yes
- A new window will open. For the ring, we'll just use the defaults. Click on the Defaults button
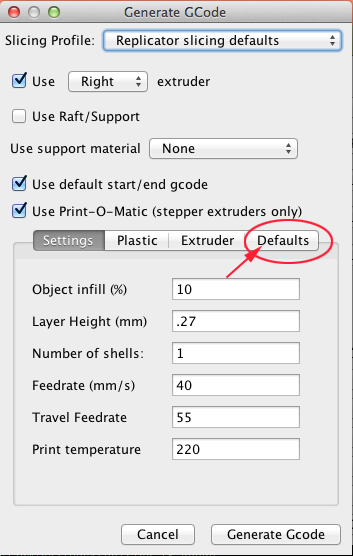
- We will be printing this project without using acceleration so pick the top option:
- Object Infill dictates the density of the print. 100% infill will make your object completely solid, while 0% will make it hollow.I've never used an infill greater than 30%. If you will be grilling into the plastic or your part will be used to do some kind of work (perhaps a gear), then sett he infill to 20-30. You can leave the Infill at 10 for the ring.
- Layer Height determines how flat each layer of your print is going to be. The default is around .3 mm, but you can experiment with layer heights as low as .1 mm (but you would have to slow down the printing) if you’re looking for finer detail. For the ring, change the layer height to .27.
- Number of shells refers to the outer structure — the thickness of the perimeter your bot prints on each layer before it starts on the infill. Every model is going to start with one shell, so the number of shells you set in Print-O-Matic is actually the number you’re adding. If you enter 2 here, your object will be printed with three concentric perimeters. These build in towards the center, so they make your object more sturdy without changing the modelled surface. Generally 1 extra shell is great. There are cases when you will even set this to 0.
-
Feedrate is the speed at which your bot moves while extruding plastic, and Travel Feedrate is how fast it moves when it's not. Again, the defaults are a good place to start, but you might want to experiment with them.
- Here's where you pick your extruder. Once you have selected your color, select the appropriate extruder.
- Now click on Generate GCode. This process may take some time depending on how complicated the model is. When it is completed insert an SD card into your computer then click on Build to file or use with SD card
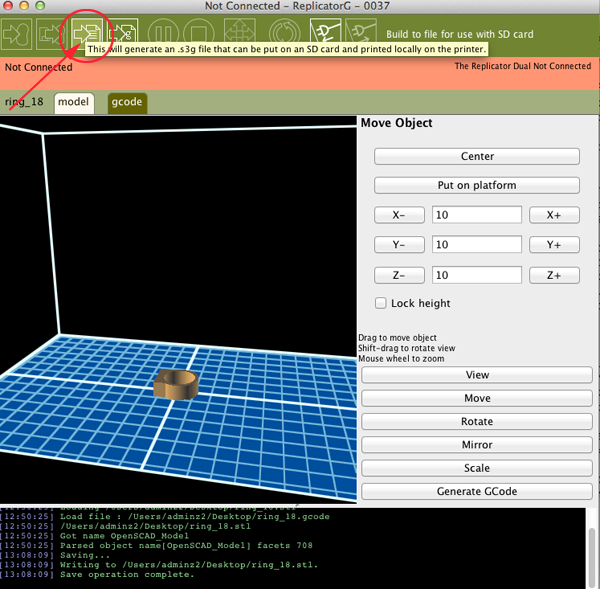
- If you are printing with PLA, you will need to adjust the Heated Build Platform temperature. Click on GCode
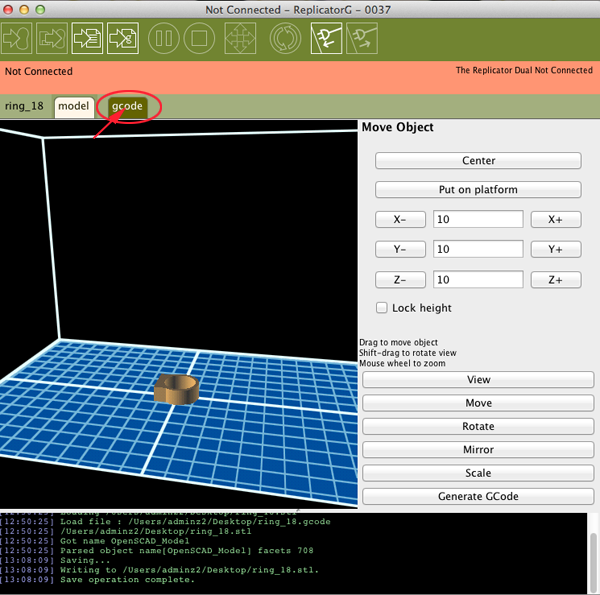
Find the line that begins with M109. Change S110 to S50.
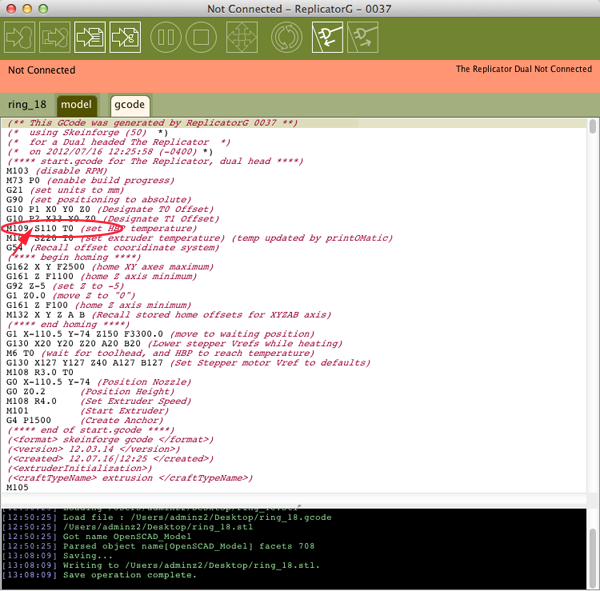
- Eject the SD card and insert into the MakerBot. From the Interface screen, select Print from SD and navigate to your file and select it. The MakerBot will begin heating and then when the appropriate temperatures are met, will begin printing.
Tinkercad
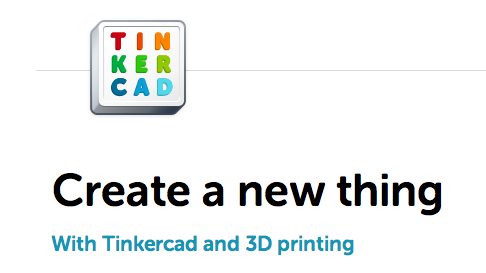
tinkercad.com
Tinkercad is a web-based 3D modeler that at its heart has three basic tools:
Add,
Subtract and
Workplane. It requires WebGL support, so you'll have to use at least Chrome 10 or Firefox 4.
Tinkercad is simple to use and allows you to build models quickly. The latest version allows you to move and rotate your models and forms after they are created. Tinkercad is continually changing. So keep an eye out for new shapes and functionality.
- To design a 3D model. Log in and click on Design then Design a new thing
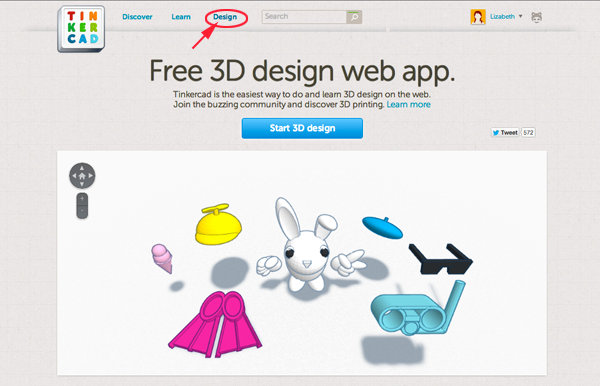
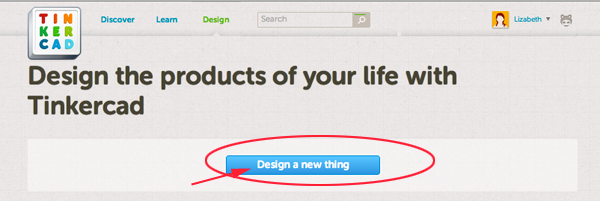
- For greater precision I change the Snap grid value to 0.1
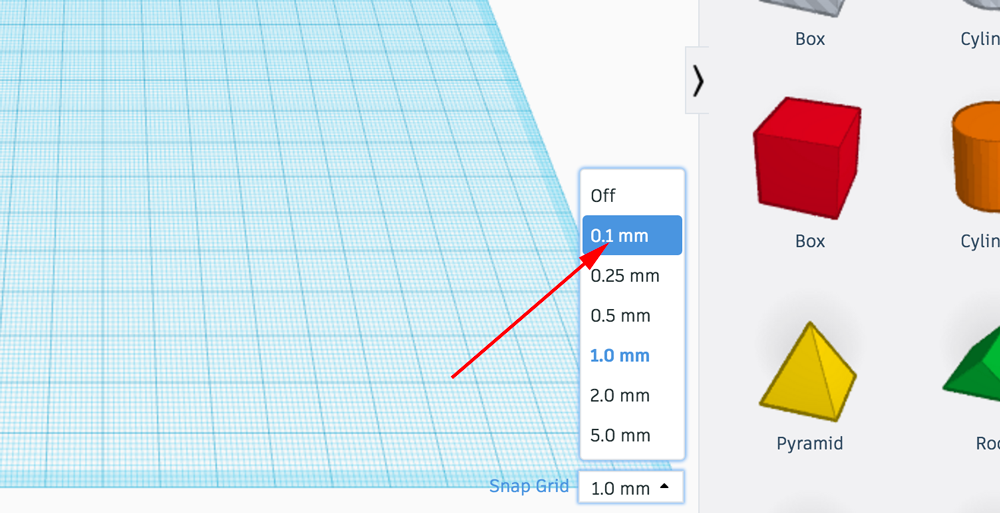
- To add shapes, letters and numbers drag your selection from the palette on the right to the workplane:
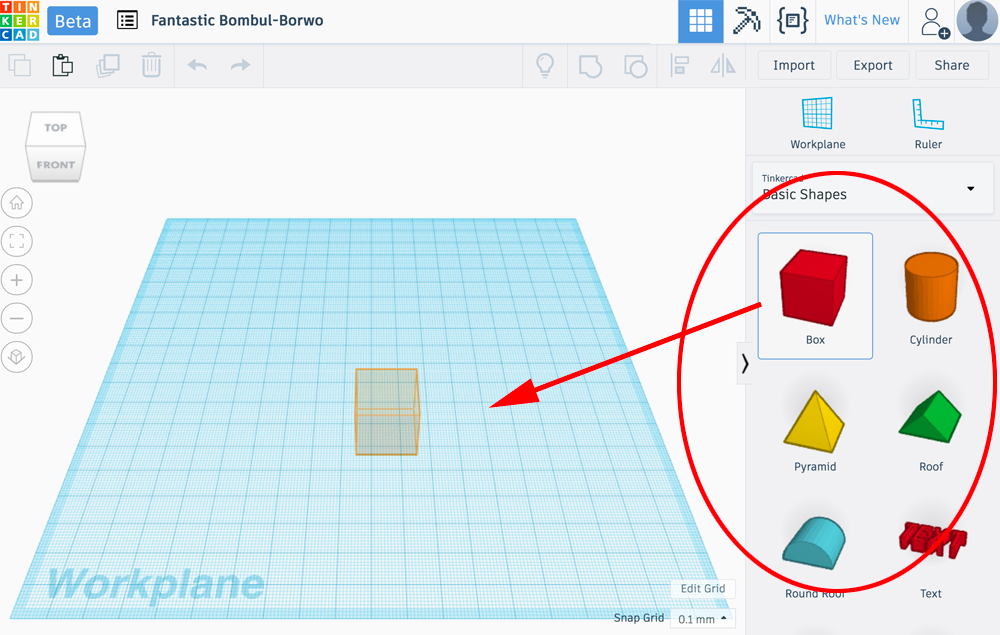
- You can get the dimensions by moving the cursor over these handles
- You can resize your form by dragging the corner points:
- Dragging the corner point while holding shift will increase the X,Y and Z axis equally:
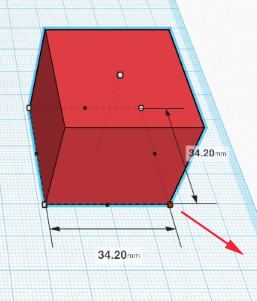
- You can copy and paste your forms using the standard keyboard commands. When you paste, Tinkercad will move your new form to the right:
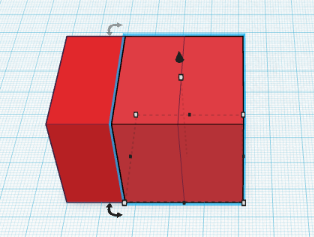
- You can raise the height of your form by dragging the node below the up arrow
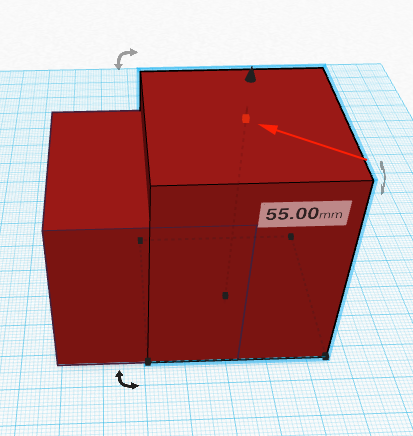
- You can subtract shapes from each other by placing the shape you want to remove, selecting it and then clicking on the the hole icon
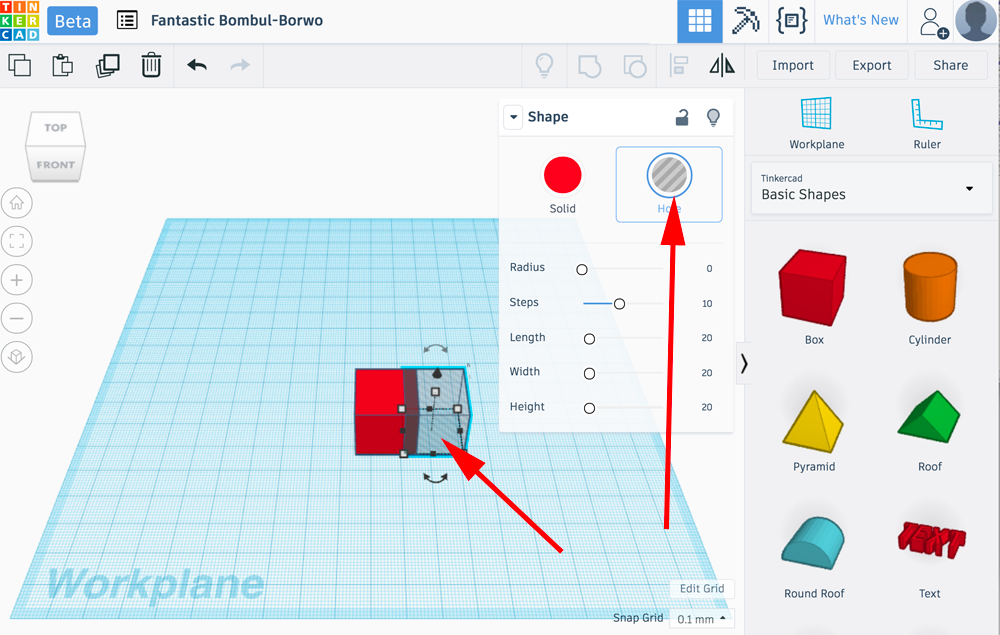
- You can still adjust the location of the hole by dragging the form
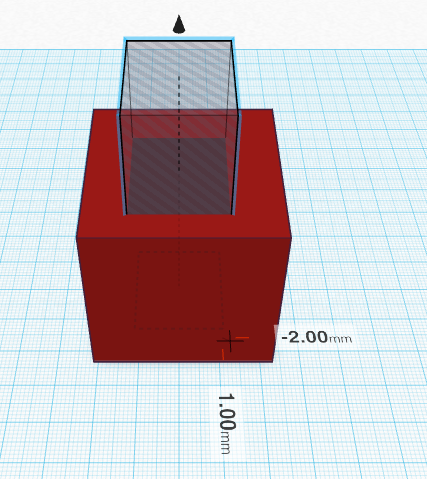
-
When you want to remove the shape, drag your cursor over both objects to select them (or Shift+Left Click)
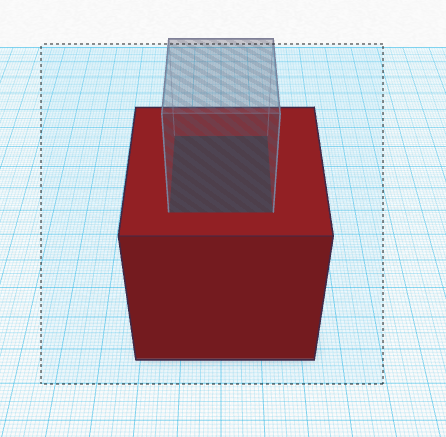
Then click on Group
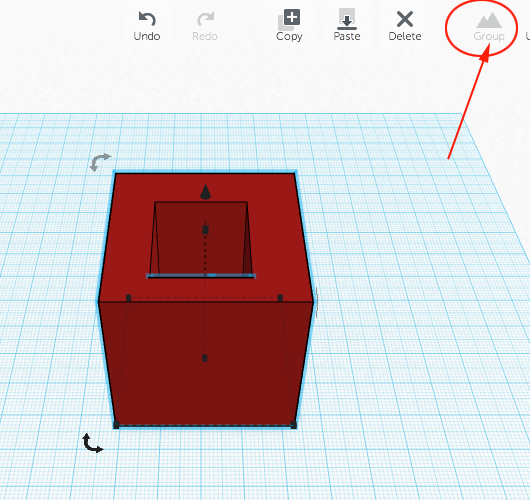
- To view the hole, rotate with the mouse
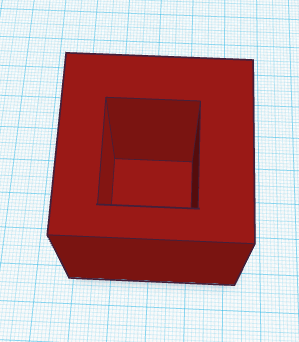
- You can easily rotate your objects by clicking on the rotation icons
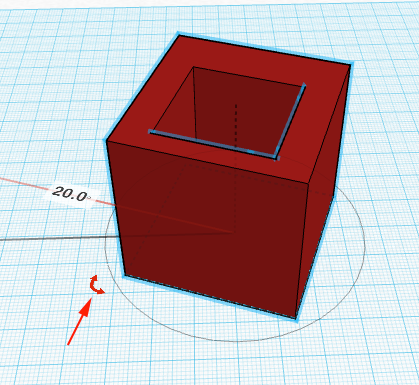
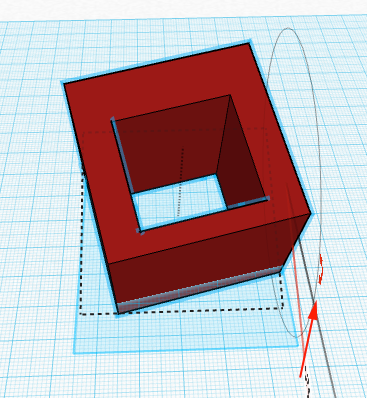
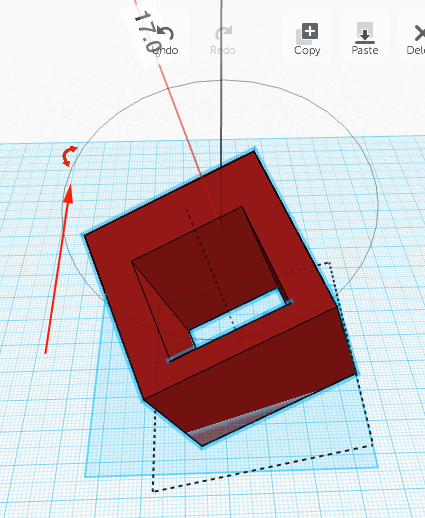
- You can move the workplane by placing it on a side of your form
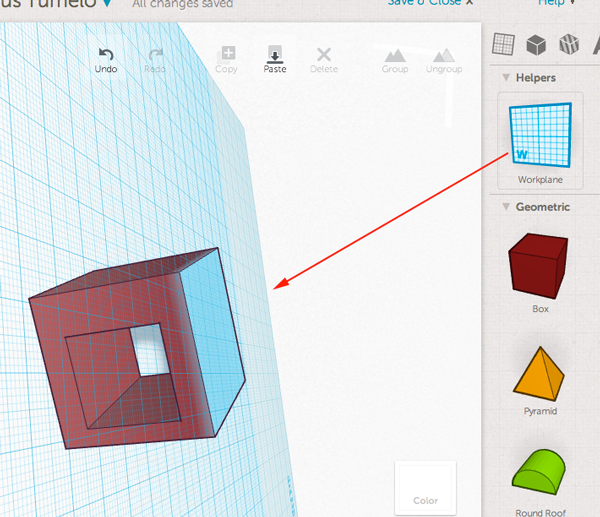
- To reset the workplane, just drag the workplane from the palette to the work area
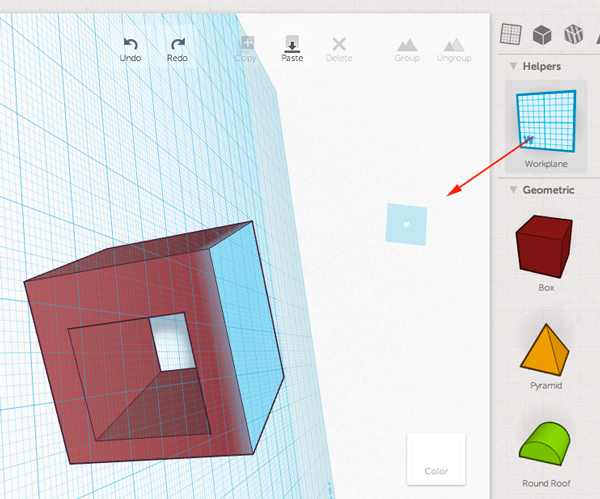
- You can measure distances using the ruler
Place the ruler then click on objects
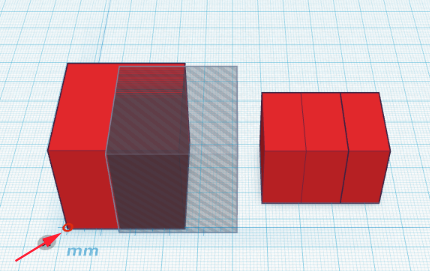
- If you select two or more shapes, clicking on this icon allows you to align your shapes
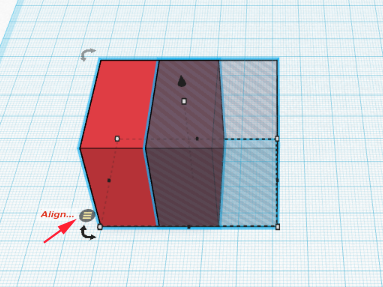
- To save the STL file, click on the Print 3D button
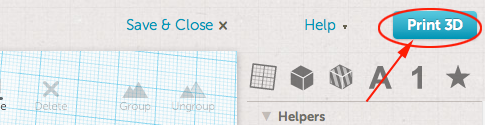
Then click on the Download STL button:
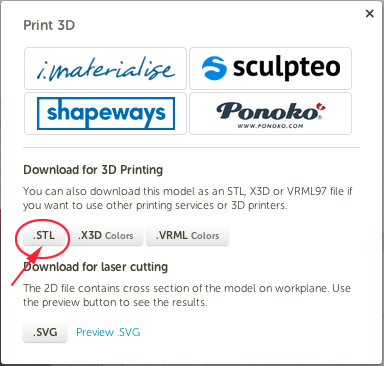
- Experiment, have fun, print
To get
Tinkercad to run on Mac with Firefox you'll have to do the following:
- Type about:config in the Firefox 4 URL bar
- Type webgl in the search box
- webgl.force-enabled = true
- Go to https://tinkercad.com and refresh the page
Background: Driver support on older OS/Graphics card combinations is bad so the browser vendors have blacklisted a number of devices. All of Mac OS X 10.5 is blacklisted in Firefox, what you did above is circumvent this blacklisting.
Windows
on Windows XP, WebGL and acceleration is blacklisted.
To enable it,
in command line:
chrome.exe --enable-webgl
or
- Close any open Chrome windows
- Find the Chrome shortcut you use (normally on the desktop or in the start menu) and right click on it.
- Select 'Properties'
- Add the '--ignore-gpu-blacklist' flag without the quotes at the end of the 'Target' box
or
- type "about:flags" on address bar of google chrome
- under "Override software rendering list" click "enable"
- scroll down and "relaunch google chrome"
Linux
In command line:
or
google-chrome --ignore-gpu-blacklist
Mouse shortcuts:
Right Click is the same as CTRL+click.
- right drag/CTRL+drag rotate the camera
- shift-right drag/CTRL-shift drag pan the camera
- mouse wheel zoom in and out
Thingiverse
Thingiverse is a universe of things.
It is also a place to share your digital designs with the world, as well as a community of people who create and share designs freely, so that all can benefit from them.
To save your own digital designs, you need to register at Thingiverse. All the information that is required is a username, email, password and human status.
Once you've registered, you can choose to fill out your profile or not.
By hitting the Email Tab, you can request emails
- Whenever someone posts a new comment on something you've designed.
-
Whenever someone posts a new comment on something you've made.
-
Whenever someone creates a derivative from of one of your things.
-
Whenever someone physically makes of one of your things.
-
Whenever one of your things has been featured.
Sometimes there are problems with downloaded files. The creator may have made the model for animation and not 3D printing or the creator may have not realized there were issues with the file. You can fix these files either using Netfabb or Meshmixer.
Netfabb
- Open Netfabb
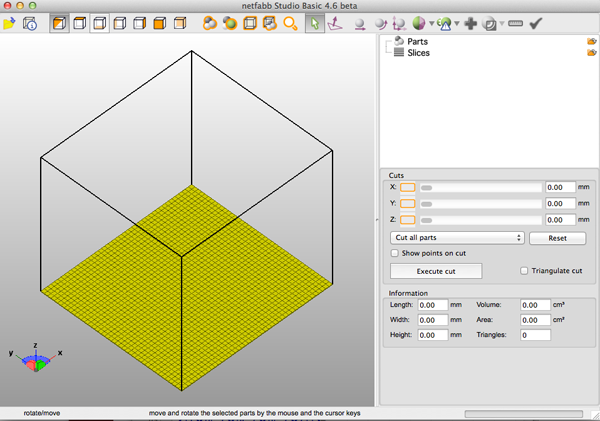
- Open the STL
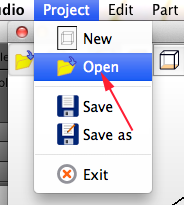
- If you have errors you will see an exclamation mark in a triangle
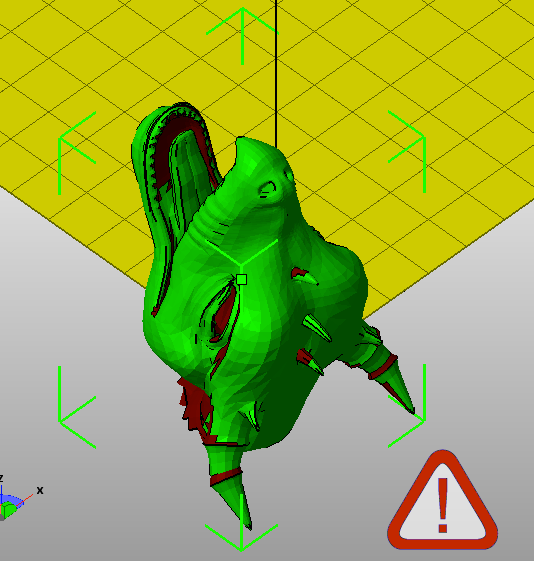
- To repair the problems click on Repair Part from the Extras menu
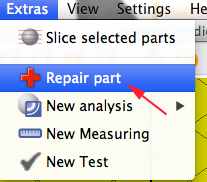
- Select Automatic Repair
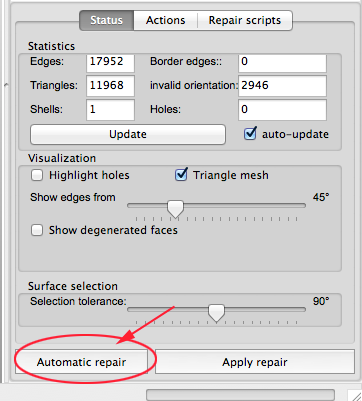
- Execute the repair:
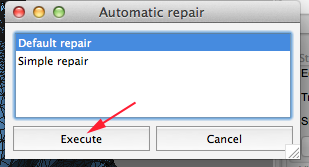
- Now Apply the repair
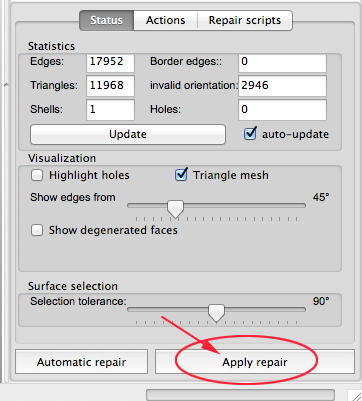
- Confirm that you want to remove the old part

- Export the fixed STL file y clicking on Part>Export>STL (binary)
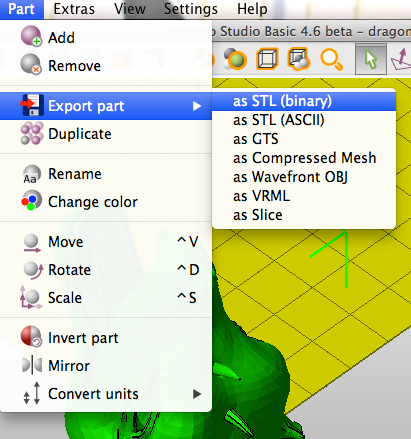
Meshmixer
- Open meshmixer.
- Click Import to open your stl.
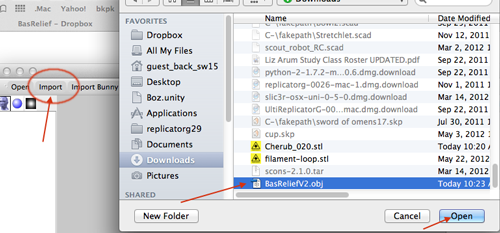
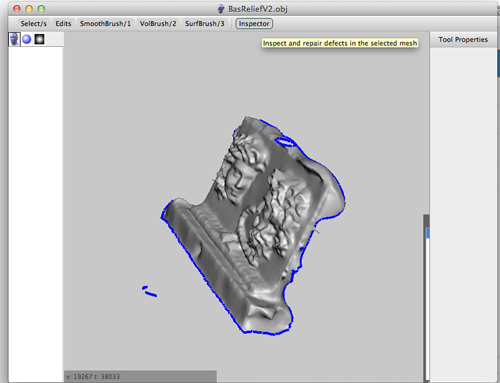
- Click Inspector.You'll see your model with a number of spheres attached to it.
Blue spheres represent holes
Red spheres represent non-manifold areas
Magenta spheres represent disconnected components
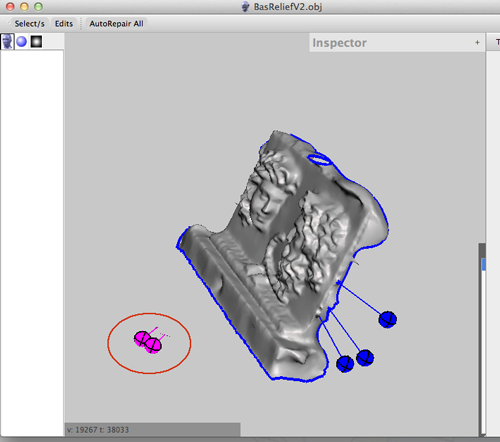
- Left clicking on a sphere will repair the problem.
- Right clicking on the sphere will select the area and allow you to edit that part of the mesh.
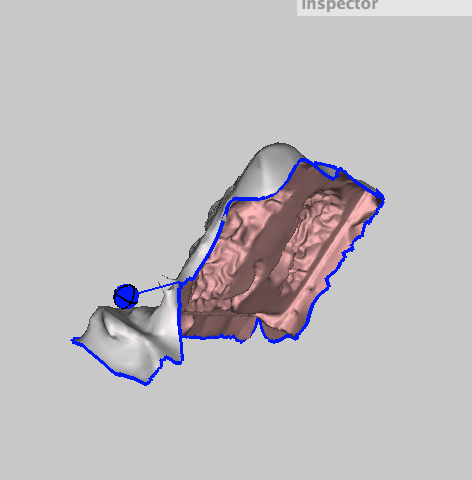
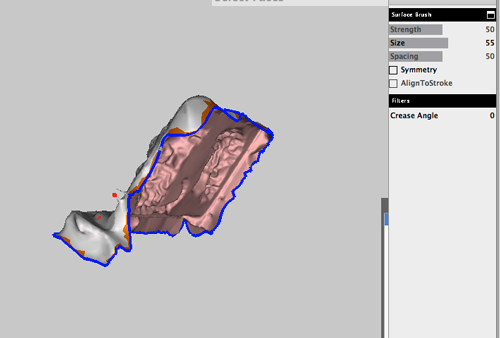
- You can use the volumetric brushes to make changes to the model:
Volumetric Bushes
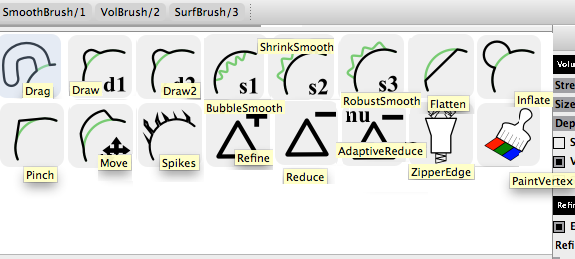
To select The Secondary brush hold down SHIFT and LeftMouse drag.
To reduce the number of triangles in the mesh:
- Select Drag
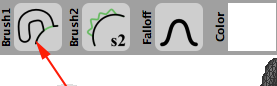
- Increase the strength of the brush
- Select Reduce and paint over the mesh
- You can also use the Edit tool:
Mirror
- Select how much of the model you want to mirror by adjusting the plane
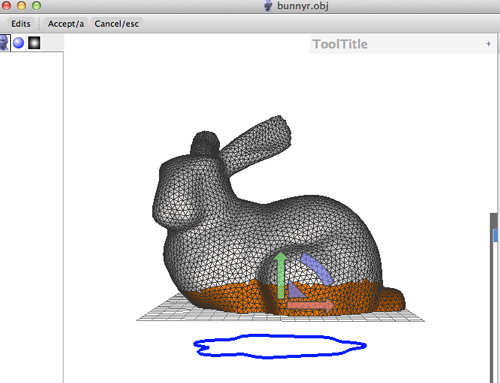
- Accept the transformation
Duplicate:
- Select Duplicate
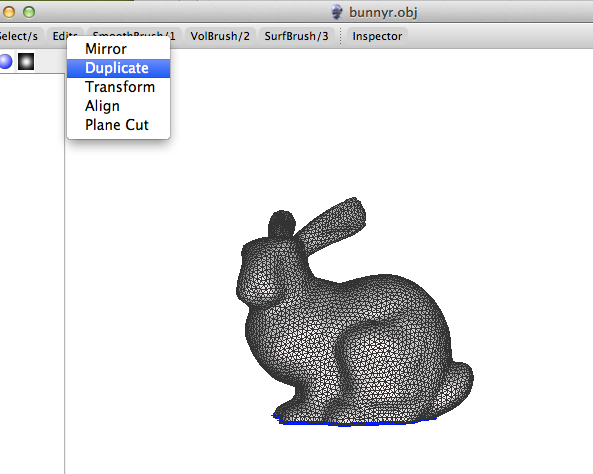
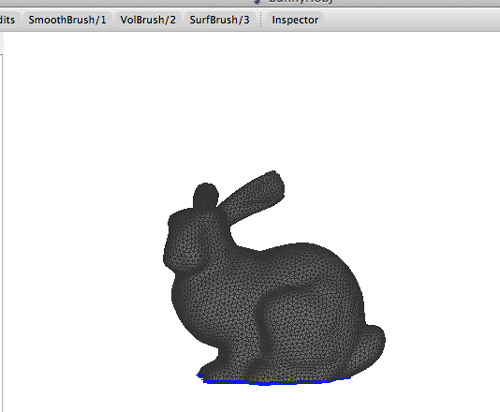
- Select Transform and move the duplicate
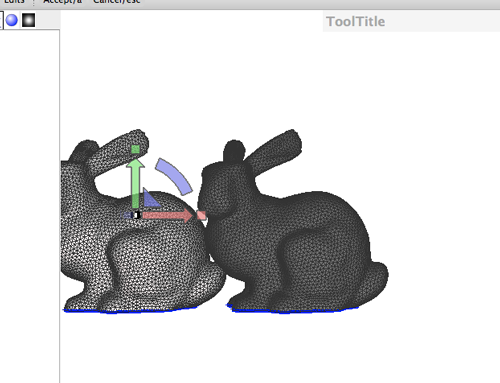
Transform:
- Select Transform
- Make adjustments (scale, move, rotate)
- Accept transformation (A)
- Repeat steps 2 and 3 until you get the necessary form.
Align allows you to change the alignment.
Plane Cut allows you to cut off and make a mesh solid by adjusting and accepting the transformation.
- You also have functions at your disposal:
Functions
Once you've made a selection there are a few things you can do:
- Erase and Fill (F). Allows you to select an area around a hole and fill it, or remesh a selected mesh.
- Discard (X). Allows you to make a selection and discard it.
- Reduce. Allows you to select the mesh and reduce the triangles.
- Remesh. Allows you to remesh a selected area.
- Extrude. Allows you extrude an area by dragging the offset selector.
- Extract. Allows you to make a separated copy of your selection
- Bridge/Handle. Allows you to create support or connect two areas by making a selection of the areas.
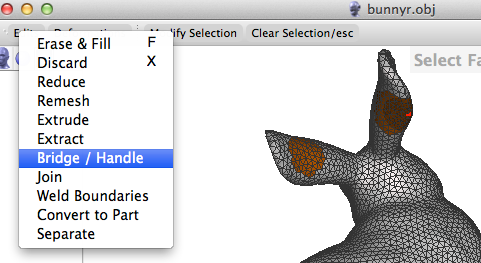
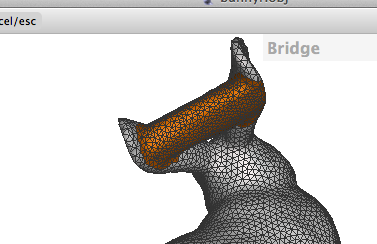
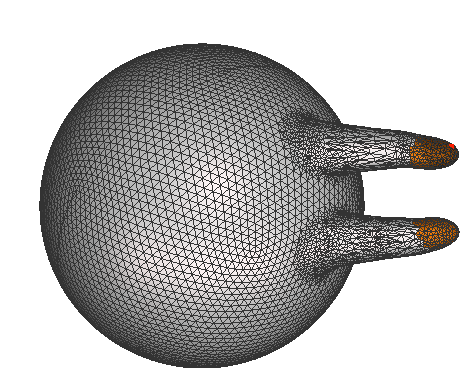
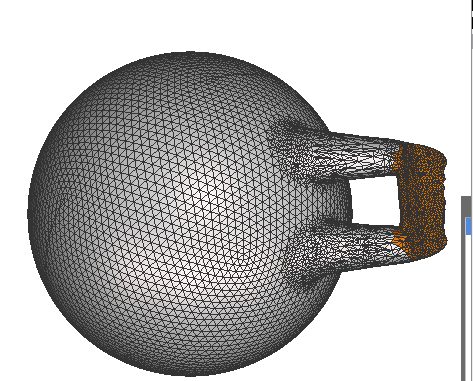
Then reduce the triangles using the the Volumetric Brush:
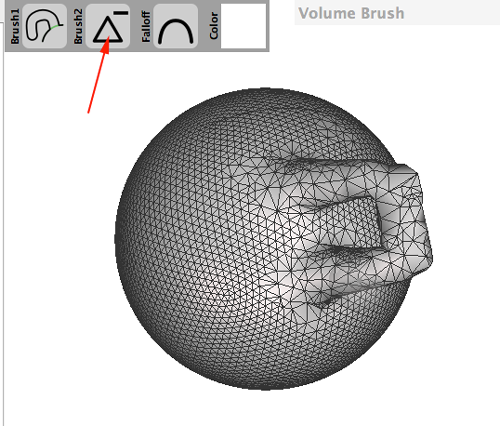
This tool also allows you to make a hole:
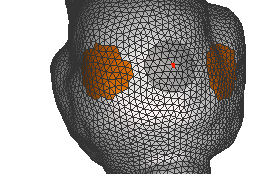
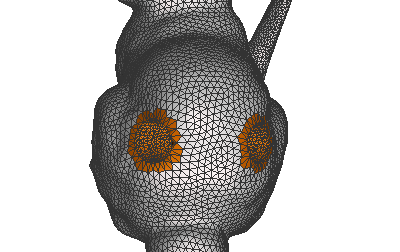
- Join.
- Weld Boundaries. Use this tool after you have used the zipper brush.
Make a selection of the area zippered, then weld the seem together. Follow this step up with the Smooth Brush.
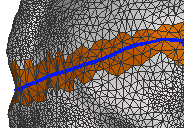
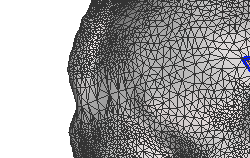
- Convert to part
- Separate. You use this when you want to combine two meshes.
- When you're done, you can export your file as an STL.